How to Optimize Your Production Line with Profile Roll Forming Machines
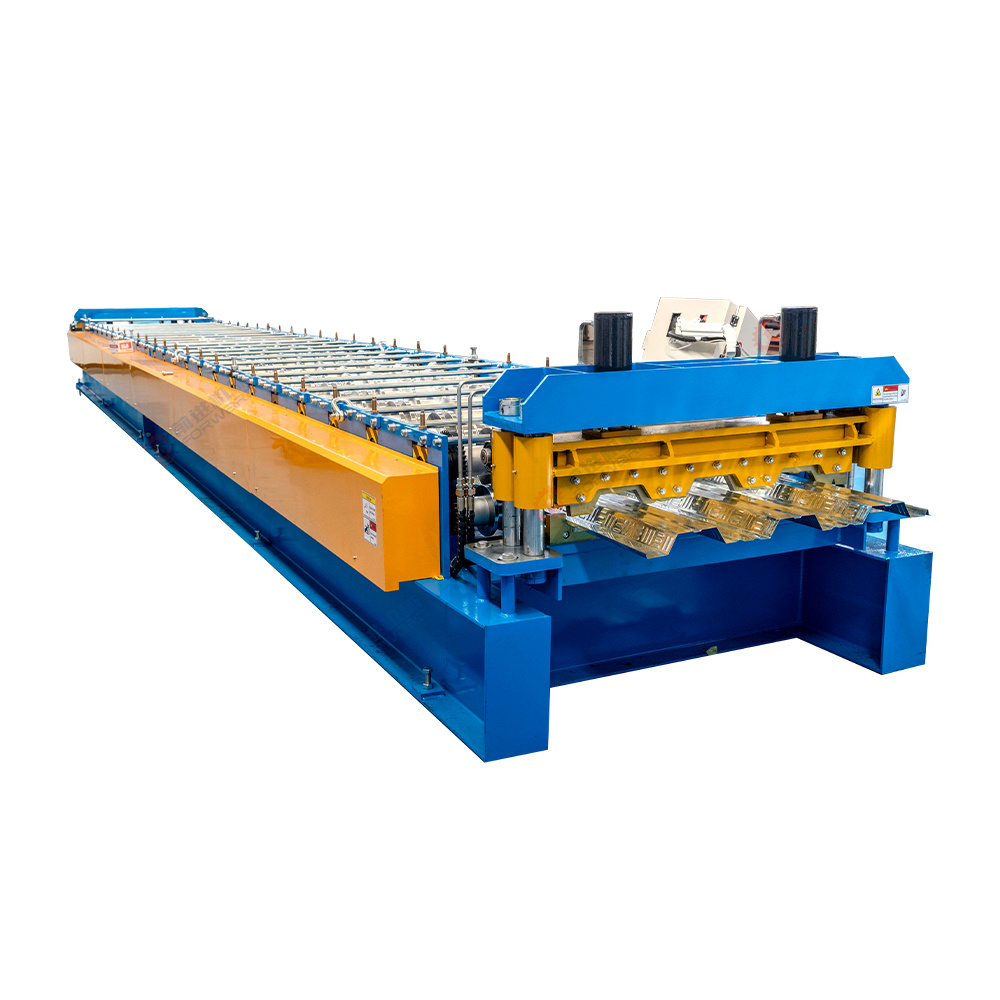
How to Optimize Your Production Line with Profile Roll Forming Machines
Understanding Profile Roll Forming Machines
Profile roll forming machines are essential tools in modern manufacturing, designed to create metal profiles through a series of continuous bending operations. These machines are capable of producing complex shapes with high precision, making them indispensable in various industries such as construction, automotive, and appliances.
### What is Profile Roll Forming?
Profile roll forming is a manufacturing process that transforms flat metal sheets into specific shapes by passing them through a series of rolls. Each roll gradually bends the material until it reaches the desired profile. This method is favored for its efficiency, repeatability, and ability to produce long lengths of uniform profiles.
### Key Components of Profile Roll Forming Machines
1. **Rolls**: The critical components that shape the metal as it passes through. They can be customized for different profiles.
2. **Feeding System**: Ensures that the metal sheet is fed into the machine at the correct angle and speed.
3. **Cut-off System**: Automatically cuts the formed profiles to the desired length.
4. **Control System**: Manages the entire operation, including speed, temperature, and pressure settings.
The Importance of Optimizing Your Production Line
In a competitive market, optimizing your production line can lead to significant advantages, including reduced costs, improved product quality, and enhanced customer satisfaction.
### Benefits of Optimization
- **Increased Efficiency**: Streamlined processes reduce production time and waste.
- **Cost Reduction**: Less material waste and lower labor costs contribute to overall savings.
- **Improved Quality Control**: Enhancements in production lead to fewer defects and higher quality products.
Strategies for Optimizing Production with Profile Roll Forming Machines
To fully leverage the capabilities of profile roll forming machines, several strategies can be implemented.
### 1. Analyze Your Current Production Process
Before making any changes, conduct a thorough analysis of your existing production line. Identify bottlenecks, inefficiencies, and areas for improvement.
#### Tools for Process Analysis
- **Flowcharts**: Visual representations of the production process can help spot inefficiencies.
- **Time Studies**: Measure how long each step takes to identify delays.
### 2. Invest in High-Quality Machinery
Not all profile roll forming machines are created equal. Investing in high-quality, modern machines can yield significant returns in productivity and product quality.
#### Factors to Consider When Choosing Machinery
- **Material Compatibility**: Ensure the machine can handle the materials you intend to use.
- **Customization Options**: Look for machines that can be tailored to your specific profile requirements.
### 3. Implement Automation
Automating your production line can significantly enhance efficiency. Profile roll forming machines often come with automation features that can streamline operation, reduce labor costs, and improve consistency.
#### Benefits of Automation
- **Consistent Quality**: Automation reduces human error, leading to fewer defects.
- **Reduced Labor Costs**: Less reliance on manual labor decreases costs.
Improving Workflow with Layout Optimization
The layout of your production line plays a crucial role in efficiency. A well-organized workspace minimizes unnecessary movement and maximizes productivity.
### Tips for Layout Optimization
1. **Minimize Distance**: Arrange machines and workstations to reduce the distance materials must travel.
2. **Create Clear Pathways**: Ensure that workers can move freely without obstacles.
3. **Utilize Vertical Space**: When possible, use shelving and storage solutions that maximize vertical space.
Training and Development for Operators
Even the most advanced machinery cannot compensate for untrained personnel. Investing in operator training is essential for maximizing productivity and safety.
### Key Training Topics
- **Machine Operation**: Ensure operators understand how to use the machines effectively.
- **Safety Protocols**: Training on safety measures can reduce the risk of accidents.
- **Quality Control**: Educate operators on how to identify and rectify defects early in the production process.
Continuous Improvement: Monitoring and Feedback
Optimization is an ongoing process. Regular monitoring and feedback mechanisms can help identify new areas for improvement.
### Establishing Key Performance Indicators (KPIs)
KPIs should be established to measure various aspects of production, such as:
- **Production Rate**: The number of units produced in a given time frame.
- **Defect Rate**: The percentage of defective products.
- **Machine Downtime**: The amount of time the machine is not operational.
Leveraging Technology in Production Optimization
In today's digital age, technology plays a vital role in optimizing production lines.
### Software Solutions
Investing in software that provides real-time monitoring and data analytics can offer valuable insights into your production process.
- **ERP Systems**: Integrate various business processes into one comprehensive system.
- **Data Analytics Tools**: Analyze production data to identify trends and make data-driven decisions.
FAQs About Profile Roll Forming Machines
**Q1: What materials can be used with profile roll forming machines?**
A: Common materials include steel, aluminum, and copper, but the machine can be tailored to accommodate various materials.
**Q2: How does profile roll forming compare to other forming processes?**
A: Profile roll forming is more efficient and cost-effective for producing long lengths of consistent profiles compared to processes like stamping or extrusion.
**Q3: Can profile roll forming machines be customized for specific applications?**
A: Yes, many manufacturers offer customization options to tailor machines for specific shapes and sizes.
**Q4: What maintenance is required for profile roll forming machines?**
A: Regular maintenance includes lubrication, checking for wear on rolls, and ensuring electrical components are functioning properly.
**Q5: How can I determine if my production line needs optimization?**
A: Look for indicators such as increasing defect rates, longer lead times, and higher operational costs.
Conclusion
Optimizing your production line with profile roll forming machines can lead to remarkable improvements in efficiency, cost-effectiveness, and product quality. By understanding the nuances of these machines and applying strategic methods for optimization, manufacturers can stay competitive in the ever-evolving industrial landscape. Implementing automation, training operators, and leveraging technology are just a few of the essential steps in this transformative process. Investing time and resources into optimization will yield dividends in the long run, ensuring your manufacturing processes are not only efficient but also sustainable.
Key words:
Previous Page
Previous Page:
recommend News
Share