Integrating Automation with Cold Roll Forming Machines: A Smart Move for Modern Manufacturing
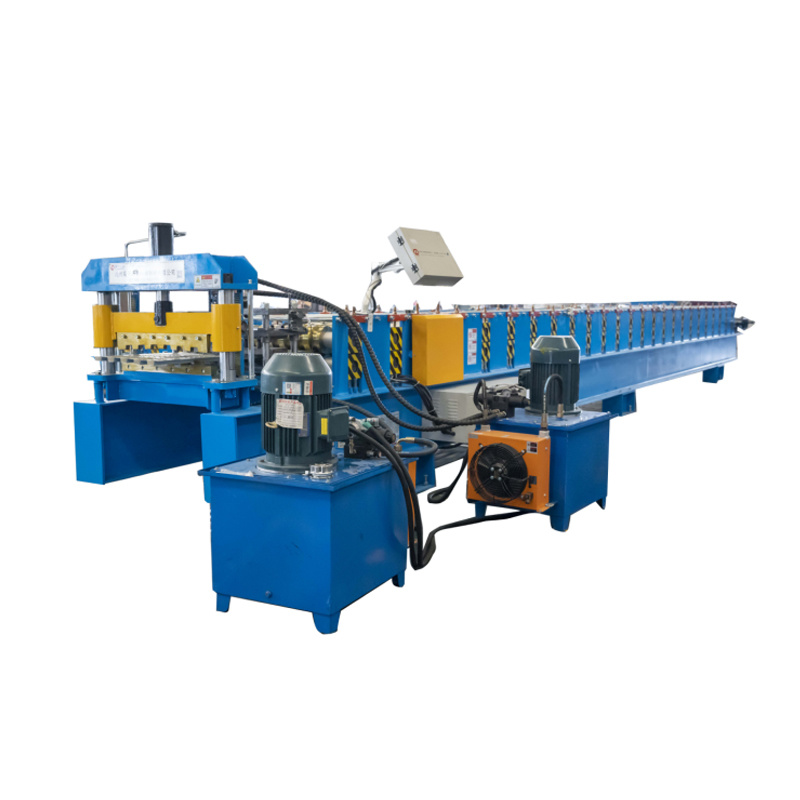
Integrating Automation with Cold Roll Forming Machines: A Smart Move for Modern Manufacturing
Table of Contents
- 1. Introduction to Cold Roll Forming Machines
- 2. The Benefits of Automation in Manufacturing
- 3. How to Integrate Automation with Cold Roll Forming Machines
- 4. Challenges of Integrating Automation
- 5. Best Practices for Automation Integration
- 6. The Future of Manufacturing with Automation
- 7. Success Stories: Companies Thriving with Automation
- 8. Frequently Asked Questions
- 9. Conclusion
1. Introduction to Cold Roll Forming Machines
Cold roll forming is a widely used manufacturing process that involves the continuous bending of sheet metal into desired shapes. These machines can produce complex profiles with high precision, making them essential in various industries, including automotive, construction, and appliance manufacturing. The ability to create lightweight yet strong components has pushed cold roll forming to the forefront of manufacturing technology.
2. The Benefits of Automation in Manufacturing
Integrating automation into manufacturing processes offers numerous advantages. Key benefits include:
- Increased Efficiency: Automation reduces the time required to complete tasks, leading to higher production rates.
- Improved Quality: Automated systems enhance consistency and reduce human error, resulting in superior product quality.
- Cost Savings: By minimizing labor costs and reducing waste, automation can lead to significant cost savings over time.
- Enhanced Safety: Automation reduces the risk of workplace accidents by taking over hazardous tasks.
- Flexibility: Modern automated systems can adapt to changes in production needs, allowing for quick adjustments to product specifications.
3. How to Integrate Automation with Cold Roll Forming Machines
Integrating automation with cold roll forming machines involves several key steps:
Assess Your Current Processes
Evaluate your existing cold roll forming processes to identify areas that could benefit from automation. Look for repetitive tasks, bottlenecks, and quality control points that can be enhanced through automated solutions.
Select the Right Automation Technology
Determine which automation technologies align with your production goals. Options include robotic arms for handling materials, sensors for quality control, and software for monitoring and managing production lines.
Develop a Detailed Integration Plan
Create a comprehensive plan that outlines how the automation will be integrated into your existing systems. This plan should include timelines, budgets, and training requirements for your workforce.
Implement the Automation Solutions
Begin the installation of automation technologies, ensuring minimal disruption to ongoing operations. This may involve upgrading existing equipment or installing new machinery designed to work with automated systems.
Monitor and Optimize the Automated System
After implementation, continuously monitor the performance of the automated system. Collect data on production efficiency, quality metrics, and operational costs to identify areas for further improvement.
4. Challenges of Integrating Automation
While integrating automation with cold roll forming machines presents numerous benefits, several challenges must be addressed:
High Initial Investment
The upfront costs associated with purchasing and implementing automation technology can be significant. Budgeting for these expenses is crucial for successful integration.
Workforce Resistance
Employees may fear job loss due to automation. Addressing these concerns through transparent communication and retraining programs can help ease transitions.
Technical Issues
Integrating new technologies can lead to unforeseen technical challenges. Having a dedicated team to troubleshoot issues promptly is essential for maintaining productivity.
5. Best Practices for Automation Integration
To maximize the benefits of automation integration, consider the following best practices:
Involve Your Team
Engage your employees in the planning and implementation process. Their insights can help identify potential issues and solutions early on.
Start Small
Begin with a pilot project to test the integration of automation in a controlled environment. This approach allows for adjustments before full-scale implementation.
Focus on Training
Provide comprehensive training for employees on new technologies and processes. This investment leads to smoother transitions and better overall performance.
6. The Future of Manufacturing with Automation
The future of manufacturing is undoubtedly intertwined with automation. As technologies such as artificial intelligence and machine learning continue to evolve, they will drive further efficiencies and innovations in cold roll forming and other manufacturing processes. The trend towards smart factories, where machines communicate and collaborate seamlessly, is already gaining traction, positioning businesses for sustained success.
7. Success Stories: Companies Thriving with Automation
Several companies have successfully integrated automation with cold roll forming machines, demonstrating the potential of this approach:
Case Study 1: Automotive Supplier
An automotive parts manufacturer integrated robotic arms into their cold roll forming process, reducing cycle times by 30% and increasing production capacity without compromising quality.
Case Study 2: Construction Material Producer
A construction material producer adopted sensor technology for real-time quality monitoring in their cold roll forming operations. This move led to a 20% reduction in defects and improved customer satisfaction.
Case Study 3: Appliance Manufacturer
By implementing a fully automated cold roll forming line, an appliance manufacturer achieved a 40% reduction in labor costs while increasing production output, enabling them to meet rising demand efficiently.
8. Frequently Asked Questions
What is cold roll forming?
Cold roll forming is a process that shapes sheet metal into predetermined profiles through continuous bending without heating, resulting in precise and strong components.
How does automation improve cold roll forming?
Automation enhances cold roll forming by increasing production speed, improving accuracy, reducing labor costs, and enhancing safety in manufacturing environments.
What are the initial costs of integrating automation?
The initial costs can vary widely depending on the complexity of the systems being implemented, ranging from tens of thousands to several million dollars.
How can companies overcome employee resistance to automation?
Companies can address resistance by involving employees in the integration process, providing training, and clearly communicating the benefits of automation for job security and growth opportunities.
What future trends should manufacturers look for in automation?
Key trends include advancements in AI and machine learning, the rise of smart factories, and increased connectivity through the Internet of Things (IoT), all of which will transform manufacturing processes.
9. Conclusion
Integrating automation with cold roll forming machines is not just a trend; it’s a strategic move towards enhancing productivity, quality, and safety in modern manufacturing. As industries evolve and competition increases, embracing automation will be crucial for staying ahead in the market. By carefully planning, implementing best practices, and addressing potential challenges, manufacturers can unlock significant benefits and position themselves for future success. The time to invest in automation is now, and those who lead the charge will undoubtedly reap the rewards.
Key words:
recommend News
Share